Sigma Aizu factory update: Magnesium machining and Sigma fp body production!
posted Tuesday, October 1, 2019 at 9:55 AM EST
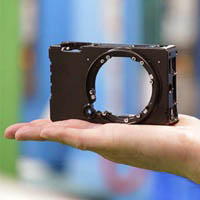
I recently got the chance to visit Sigma Corporation's lens (and camera) factory in Aizuwakamatsu Japan again. As part of the big product announcement for the new Sigma fp full-frame mirrorless camera, they invited myself, Carey Rose from DPReview and Johnnie Behiri from Cinema5D to attend, and brought us to Aizu for a tour of their factory afterwards. You can read about the new Sigma fp camera on our review page; this story will be about the factory tour.
This was actually the third time I've been in this factory; in fact the article I wrote about it back in 2013 was the first really in-depth factory tour article I'd done. You can read that account here: A geek’s tour of Sigma’s Aizu lens factory: Precision production from the inside out. On my second visit a couple of years later, I got the low-down on their lens testing process, using their custom-built "A1" test systems; that story is here: Sigma’s key to quality? Our exclusive look at the A1 system reveals all!
My original tour article went through the entire lens manufacturing process at Aizu, from top to bottom. Sigma's Aizu factory is one of the most vertically-integrated lens factories in the world; every part of the process apart from raw glass manufacturing and metal casting happens within a single facility. If you've ever wondered how lenses are manufactured, you should check it out! (It's pretty ... uh ... "detailed" ;-)
Most of what's in the Aizu factory is similar to what was there the last time, so I won't repeat my previous tour, but just refer you to that earlier article instead.
What is new is that Sigma added an on-site facility for machining and processing magnesium just last Fall (2018). This is a big deal because magnesium literally can catch fire while you're machining it if you're not careful! If things do go south, magnesium burns very, very hot. Not only that, but pouring water on a magnesium fire only makes it burn even faster, and even CO2 fire extinguishers just fuel the blaze!
The potential risks involved meant that Sigma hadn't previously machined magnesium in-house, but as they've used more and more of it in their lens barrels, and particularly with the fp camera bodies coming down the pike, it made sense to bring magnesium machining in-house.
Since they'd need more floor space to accommodate this, they decided to house their magnesium processing in a completely new structure, located a short distance from their main factory complex. That way, if something ever went seriously wrong there, they wouldn't have to worry about it burning down their entire factory complex.
This story is mainly about Sigma's new magnesium-processing facility, although I also talk some about plastic injection molding, which got rather short treatment in my earlier article.
Read on for an update on the new developments in the Aizu factory, including some shots of fp camera bodies being machined!
(By the way, special thanks to Carey Rose and friendly competitor DPReview for the photos below; I ended up losing all of mine from the tour through a piece of unbelievable stupidity that I won't bore you with here; let's just say I'll never ever format a memory card on a trip, ever again :-0 Be sure to check out Carey's own coverage of the factory tour.)
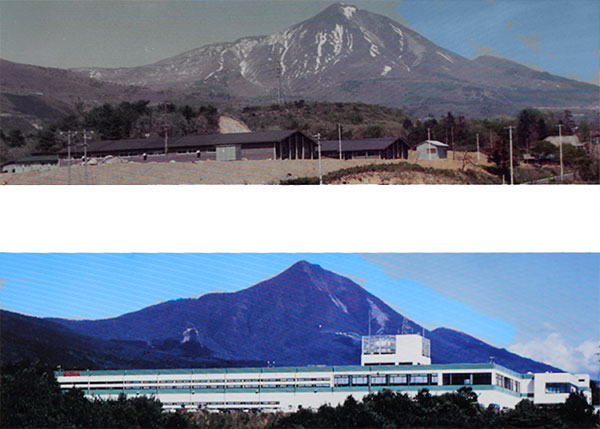
Sigma's Aizu factory has grown incredibly since it was first established in the early 1970s. (Actually, company founder Michihiro Yamaki once told me that the beginning of manufacturing in Aizu was just a few pieces of machinery in individual workers' homes. Read my original article for the funny story of how that came about :-)
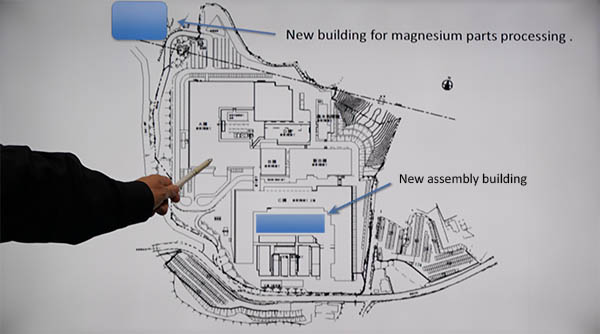
The Sigma factory continues to expand; I saw many more production machines in various areas than the last time I visited a few years back. As mentioned above, they've built a whole new building just for magnesium processing, another new one is going up in a former parking lot, and a third is planned for construction by the end of 2020.
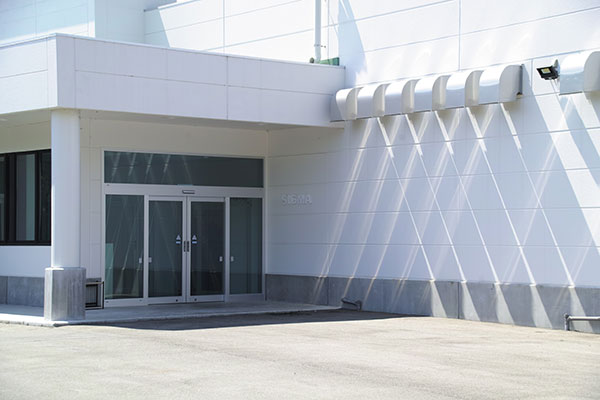
The new magnesium-processing facility presents an unimposing demeanor at its main-level entrance, but there’s actually much more to it than meets the eye.
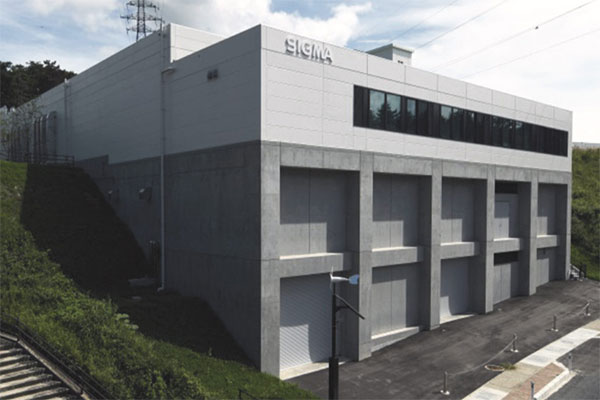
This is a view of the rear of the magnesium-processing building. It’s built into a hillside, so the back is a good three stories tall. When I asked, I was told that the lower level was for chemical processing, for different surface treatments of the magnesium. (I gather it’s akin to anodizing for aluminum.) I don’t know how tall the chemical processing area is, but it either occupies two floors or is two stories high.
At high-enough temperatures, magnesium is extremely flammable in air. Don't worry about your camera or lens spontaneously igniting, though; the autoignition temperature is 883°F/473°C :-) The thing is, if it isn't continuously flooded with coolant during machining, the chips can catch fire, and once ignited, it's extremely difficult to put out. Water only makes matters worse, and even CO2 fire extinguishers are useless, since magnesium can burn in pure CO2.
While machinery used for processing magnesium completely floods the workpiece with coolant, there's still some finite risk of things going awry -- and if things go wrong in a factory full of magnesium castings, they could go very wrong indeed. For this reason, Sigma put their new magnesium processing facility in an entirely separate building, located some distance from the rest of the complex.
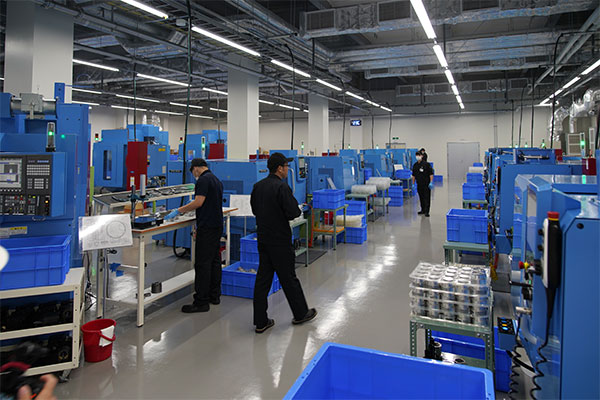
This shot shows just a portion of the magnesium machining area. The scale is pretty impressive, especially considering the cost of sophisticated CNC machining centers like the ones in the photo. :-0
The magnesium processing building is two (three?) stories, built into the side of a hill. The lower level is a chemical processing area, used for surface treatments akin to anodizing with aluminum.
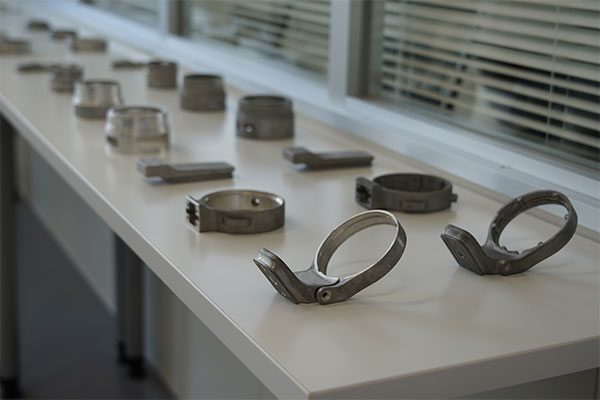
This shot shows some of the components Sigma produces. Raw castings from outside providers are trimmed to size, holes drilled and tapped, etc. I was very surprised by how much material was removed from some of the pieces. The finished parts were quite a bit lighter than the original castings.
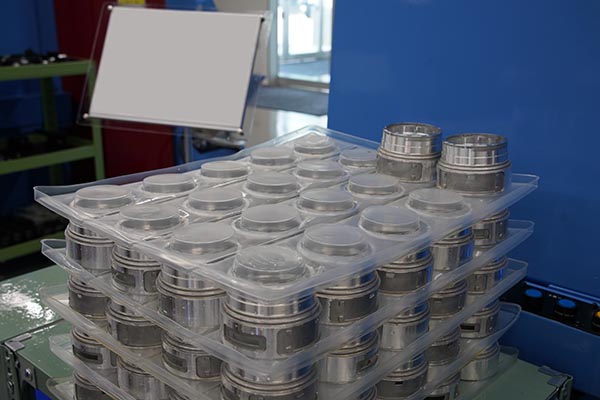
Most parts require multiple operations to reach their final forms, so there are stacks of in-process parts everywhere. This is a batch of lens-barrel components. They've already been turned on a lathe, and are now awaiting another process. (In this case, a milling operation on the machine in the next shot below.)
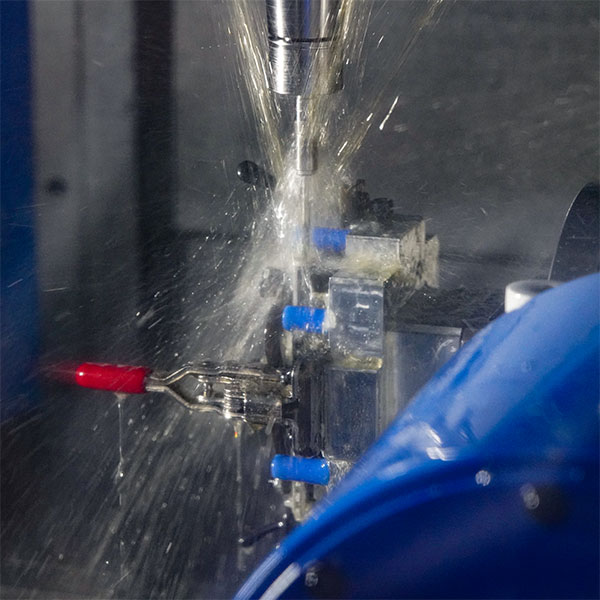
Did I say you need to use a lot of coolant when you're machining magnesium? Most machining operations use coolant, often as much for lubrication to produce a nice surface finish as for cooling. The magnesium processing machines have intense jets of coolant, often striking the workplace and cutting tool from multiple directions. This is a CNC milling machine, where the part is held stationary while a rotating cutting tool removes material. (In contrast, a lathe rotates the workpiece and a stationary cutting tool shaves off the metal.)
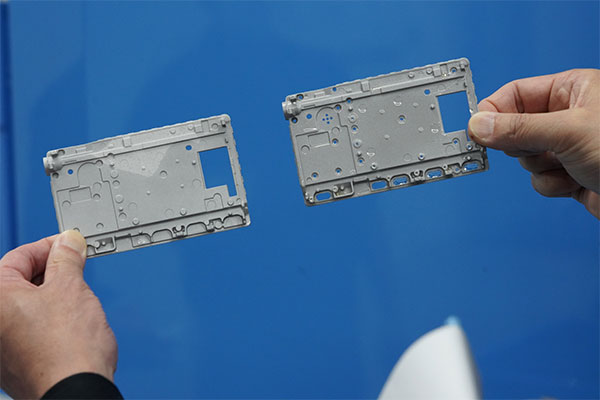
Being able to do their own magnesium processing was an important part of cost control for the new Sigma fp camera, which has a central frame made of that material. This is a before-and-after shot of an fp chassis. If you look closely, you'll see that the part on the right has a number of holes drilled through it that aren't present on the raw casting on the left. Some are drilled all the way through; others only partway, with threads tapped to receive screws.
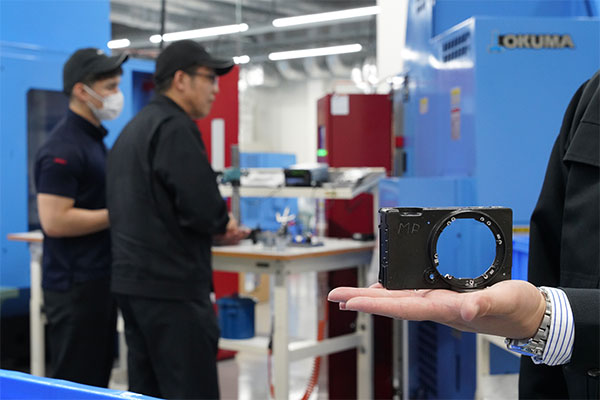
The fp has a magnesium central core, but aluminum front and rear panels. This is a front panel that's used in the magnesium facility as a template to quickly check whether the chassis pieces are correctly to size or not.
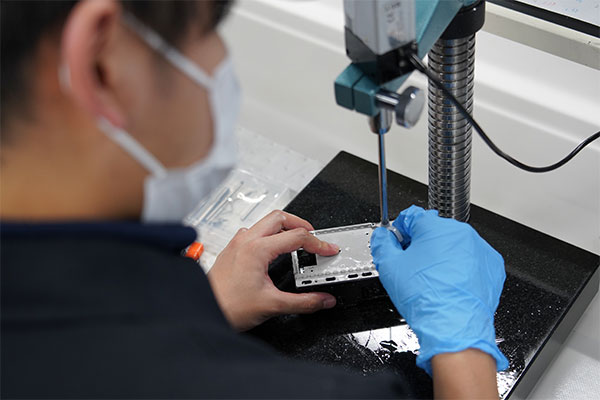
Of course, Sigma doesn't just rely on test-fitting to ensure things are in tolerance or not; they also use precise measuring instruments like the one in the picture. This is an electronic device, but the factory was virtually littered with conventional micrometers and calipers, and workers seemed to use them fairly regularly to spot-check their machines' output.

This is the storage area for incoming castings. Given the pace at which the machines seemed to crank out parts, this must be only a day or two's supply. That would make sense, both for just-in-time inventory control and for the sake of safety.
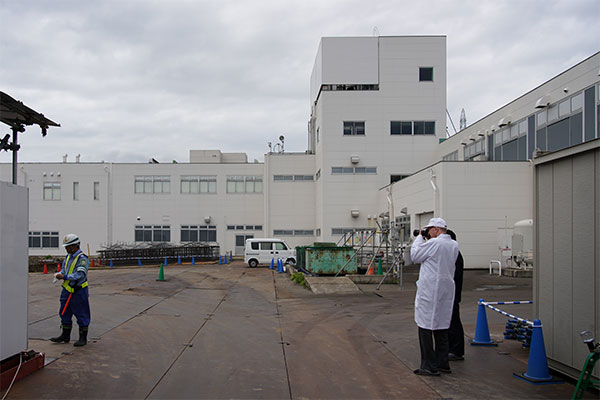
This is part of the former employee parking lot where the new assembly building shown on the site plan above is being constructed. It's just at the stage of site preparation now, but will be finished and in operation before the end of next year.
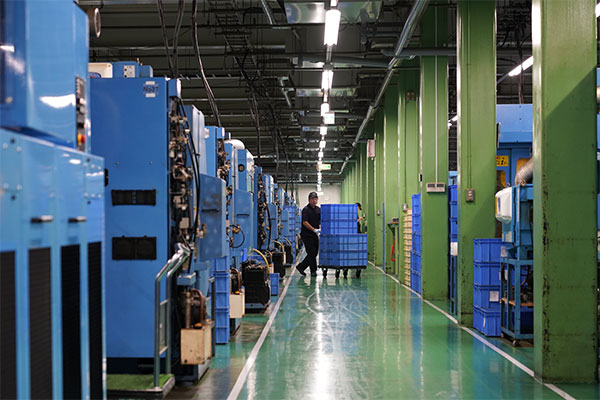
This is back in one of the main factory buildings, and shows just a tiny portion of the number of metalworking machines in the factory. The scale is incredibly impressive.
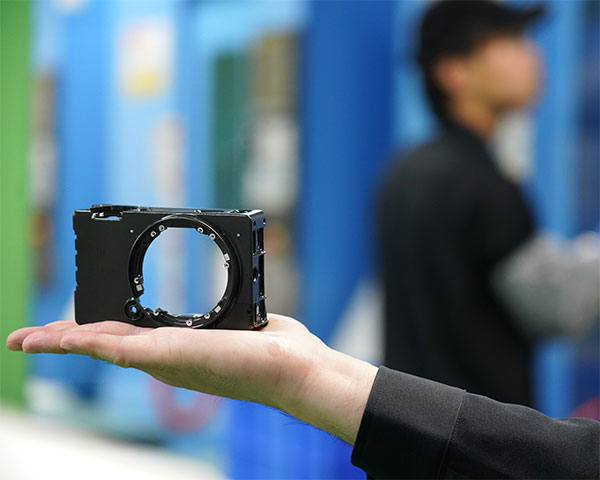
Here's an fp front panel after machining. You can see the holes that have been drilled and tapped around the flange mount.
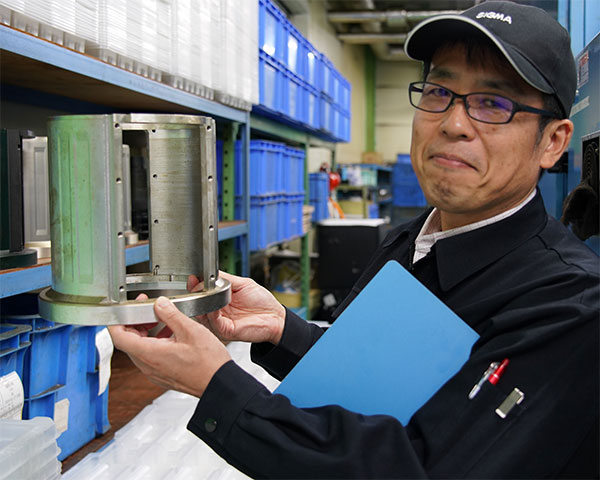
Here's the largest metal component made in the factory. It's a lens barrel from Sigma's enormous 200-500mm f/2.8 zoom lens. (That thing is huge; this is just a part of the barrel for it!)
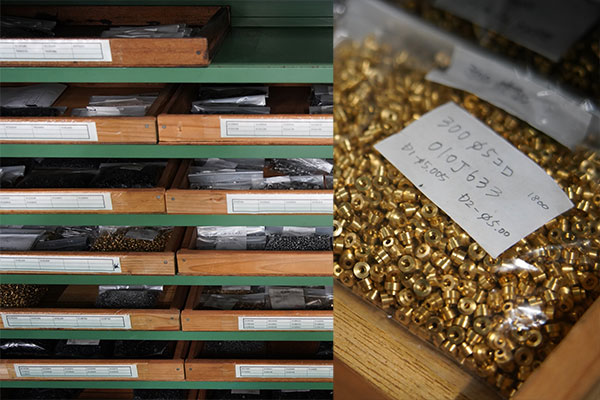
In my original Sigma factory tour article, I had a shot of the special screw-manufacturing machines that Sigma uses to make custom screws for their lenses. They use standard off-the-shelf hardware wherever possible, but in many cases they need special screws with unusual head profiles or other characteristics that can't be found in commodity parts.
What I hadn't appreciated before was just how many different types of screws they need to inventory. The shots above show just a small portion of their screw inventory area. There's drawer after drawer, packed with bags of tiny, tiny screws. They must have an inventory of hundreds of thousands of individual screws. Meanwhile, each of the banks of machines spits out a fresh screw every few seconds, non-stop.
Injection molding machines
This is an area that's incredibly important to Sigma's lens production, but one that got less than its share of attention in my previous tours of the Aizu factory. People often think that "plastic" means "cheap", but it turns out that plastic has a lot of desirable characteristics, particularly some of the specialized structural plastics which Sigma uses in various places in their products.
On an earlier tour, Sigma CEO Kazuto Yamaki told me that their plastic molding can hold tolerances of just a few microns. That's pretty incredible, given that a micron is 0.001 millimeter. (About 40 millionths of an inch!)
This time we had a bit more time around the plastic molding area, so I can share a bit more about that process with you here.
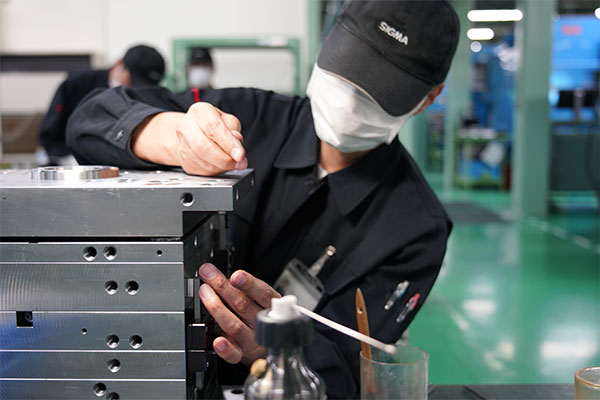
Plastic injection molding starts with the molds themselves. These are enormous blocks of stainless steel, usually a multi-layer stack of blocks that have to be carefully assembled before being loaded into the injection-molding machines. The worker here is assembling one such stack. The multiple layers are necessary both for the molding process itself, so plastic can be injected at multiple points, and for the sake of being able to separate and remove the part once it's cooled and hardened.
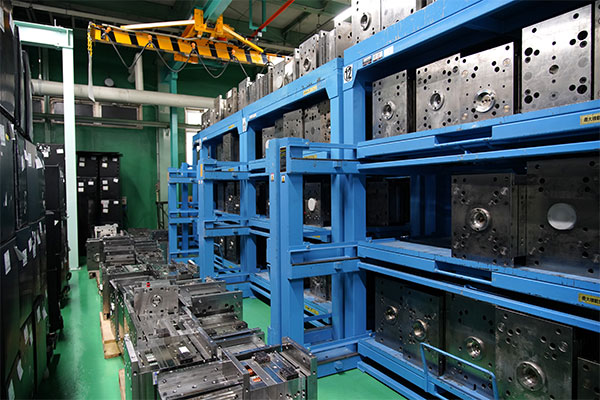
When I first toured the factory, I was struck by the fact that injection molds seemed to be just everywhere; Sigma's huge range of lenses require an even larger number of molds, given that any individual lens may have many individual molded parts making it up. This is a shot of just a tiny, tiny portion of the current mold inventory. Things didn't seem as over-crowded this time as they were when I first toured; I think Sigma has added more factory space over the year since that first visit. But the storage problem is an enormous one. I don't know how much one of these mold stacks weighs, but they've got to be at least 500 kilograms each. (Stainless steel weighs 8,000 kg per cubic meter; some of the larger mold stacks must be a half a meter on a side, so that'd be 2,000 kg.) :-0
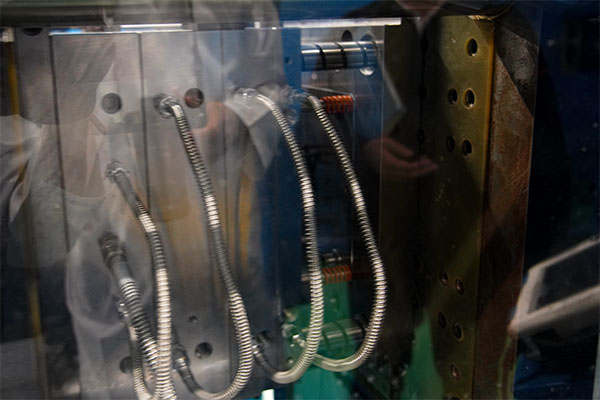
This is a shot of one of the injection machines actually molding a part. I think the metal tubes you see here are for cooling water; the mold needs to cool the melted plastic after it's injected, so it will solidify. The molten plastic is injected into the mold cavity under high pressure (anywhere from 4,000 to 16,000 psi). The hot plastic is injected at multiple points to insure that the liquid plastic flows into all the parts of the mold cavity evenly. Of course, those thousands of pounds per square inch of pressure are also pressing against the mold itself, trying to force the ends apart. To counter this, injection molding presses have huge hydraulic cylinders pressing the mold parts together. Depending on the size of the parts they're set up to mold, injection presses can exert many tons of force to hold the mold stacks together.
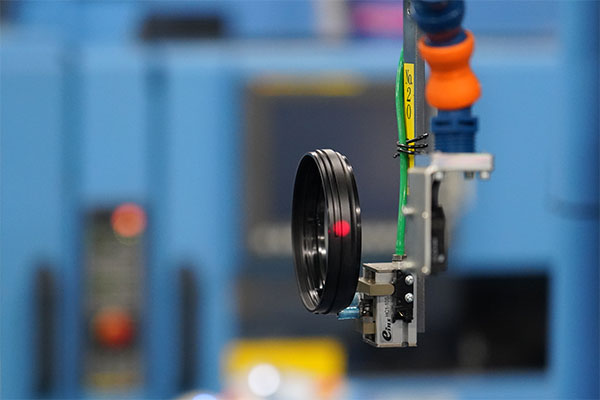
Once the hot plastic has cooled and hardened, the mold stack separates and the part is either kicked out into a bin, or as shown here, picked up by a robotic arm to be transported and stacked into a parts carrier. The red dot you see here is from a light beam that's used to make sure that the robotic handler successfully picked up the part.
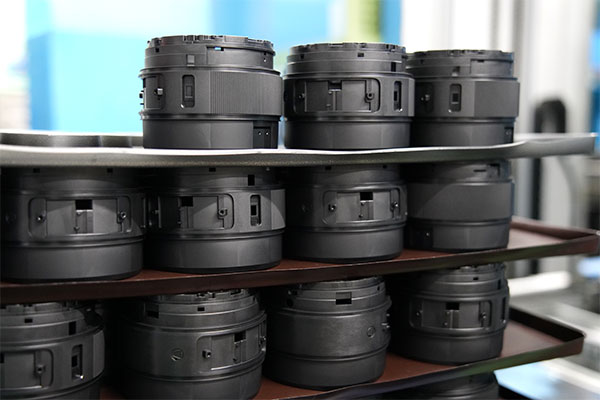
Here's a stack of parts that have just come out of a molding machine. I'm amazed by the complexity of parts that can be molded as a single piece. It's not surprising that they can have a lot of fine detail; that's pretty much a given with injection molding of plastic. The part I couldn't figure out was how the heck they got some of these out of the mold once the plastic has solidified. Think about it; anywhere there's a recess in the part means there's a corresponding projection on the mold and wherever there's a projection on the part, that means it's fitted into a recess in the mold. So the pieces of the mold have to separate out from the part anywhere there are indentations or projections.
I'm honestly baffled by this. I can imagine that some of the pieces of the mold actually retract out from the molded part (the molds after all are huge chunks of solid stainless steel), but even allowing for that, I couldn't figure out how some parts like the one above can be made. (Are there any readers out there who have experience with injection molding? If so, please chime in with your thoughts in the comments below, and share a little insight into how parts like the one shown above are created.)
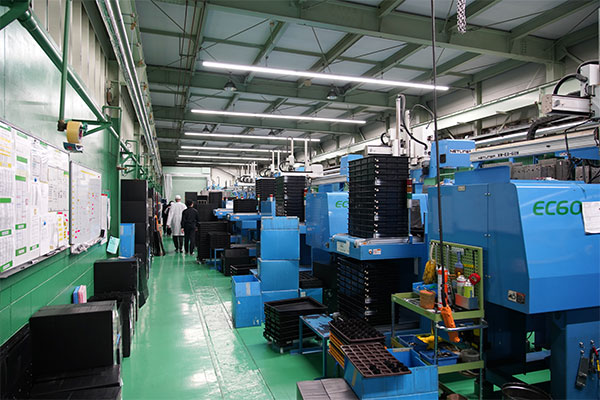
Here's just part of one row of injection molding machines in the Aizu factory. I don't know how many of these machines Sigma has altogether, but just from what we saw, I'd estimate this is only a quarter to a third of the total. I didn't think to time it while I was there, but I'd guess that a typical molding cycle takes 15-20 seconds from start to finish. So each machine kicks out several parts per minute, without pausing, for hours at a time. (They also run the molding machines across two shifts of human workers, so they have a lot of capacity to crank out molded parts.)
Summary
Sigma's Aizu factory is an amazing place, in the most literal sense of the word. As far as I know, it's the most vertically-integrated lens production facility in the world, incorporating essentially every part of the lens fabrication process, short of making the optical glass and metal casting. I could be wrong, but think the addition of a magnesium-processing facility on-premises is unique in the lens manufacturing world.
This article covers just a tiny part of the overall lens manufacturing process in Aizu; check out my original article about the factory, A geek’s tour of Sigma’s Aizu lens factory: Precision production from the inside out, from almost six years ago, for a complete start-to-finish tour of the entire production process.
Sigma has also invested a lot in final testing and quality control, with their internally-developed A1 testing system. Every single Global Vision lens -- that's their Art, Sports and Contemporary models -- is tested as it comes off the production line, to make sure it meets specifications. You can read about that system in my article from 2015, titled Sigma’s key to quality? Our exclusive look at the A1 system reveals all Again, while I don't know the intimate details of other companies' final QC testing, as Sigma has given me unparalleled access compared to any other lens maker, I don't think any other company's final QC testing of lenses goes as deep as Sigma's does.
Sigma is a truly unique company in today's world. They grew from a very modest beginning to a global optical powerhouse, while still remaining essentially a family business. (After all these years and despite their size and global footprint, they're still privately held.) This translates into a very different corporate personality and ethos than you'll find in most public companies. I don't think any other photo company has the kind of relationship with its employees that Sigma does: CEO Kazuto Yamaki and his father before him have gone to extraordinary lengths to keep production in Japan at their Aizu factory, resisting the lure of offshore production and the low labor costs associated with it. I can't translate it directly into product characteristics, but it's clear when visiting their facilities that Sigma's employees appreciate and return that sense of loyalty to the company and the products they create. And before you say "of course, you were touring the facility with the Big Boss", I can say that that's also been true of tours I've had of other factories. While the loyalty of Japanese workers to their employers is legendary worldwide, the sense of partnership and personal relationship I sense between Sigma's Aizu workers and the company itself really seems special by any measure.
As with any company, Sigma's fate ultimately rests on the quality of its products, their pricing, and whether they can stay competitive in the marketplace. Fortunately for Sigma, their employees, and all the photographers who use and enjoy their products, Sigma's unique approach seems to be accomplishing just that.

